
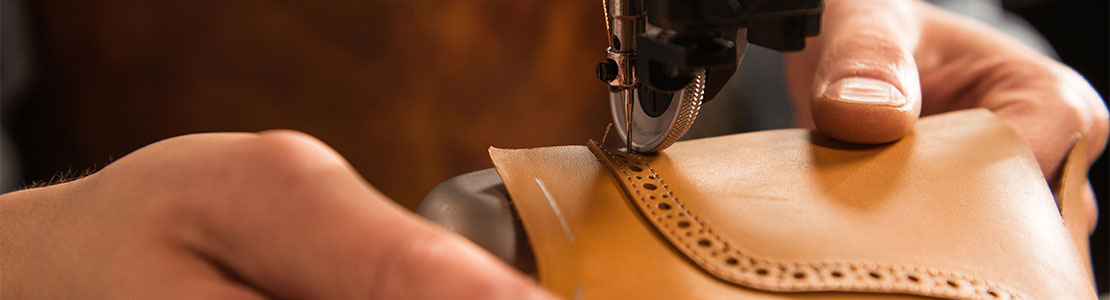
When we think of the leather industry, we often picture skilled artisans crafting fine leather goods. However, there is a critical component that plays a large part in the production process that is hidden behind the scenes: air compressors. These mechanical workhorses provide the required power and precision to ensure that leather production runs smoothly.
Understanding Air Compressors
Before we get into the role of air compressors in the leather industry, let's define what they are. An air compressor is a device that turns power into potential energy that is stored in compressed air. This compressed air can then be employed in a variety of industries, including the leather industry.
Types of Air Compressors
There are different types of air compressors, each tailored to a certain application. The following types are often used in the leather industry:
Reciprocating Compressors
The reliability and versatility of reciprocating compressors are well known. They compress air using a piston and cylinder and are commonly used in leather workshops for tasks such as cutting, stitching, and stapling.
Rotary Screw Compressors
These compressors are extremely efficient and produce a constant supply of compressed air. Rotary screw compressors are used in leather manufacturing units for larger-scale processes such as molding and pressing.
Centrifugal Compressors
Centrifugal compressors are suited for high-volume applications in the leather manufacturing industry. They deliver a continuous and high-flow rate of compressed air, making them ideal for painting and finishing jobs.
How Air Compressors Benefit the Leather Industry
Air compressors play a pivotal role in leather production for several reasons:
Cutting and Sewing
Precision is key in the leather industry. Air compressors drive cutting machines and sewing machines, ensuring that elaborate designs and stitching are accomplished precisely.
Stapling and Riveting
Stapling and riveting are important methods for attaching various components of leather products. These tools are powered by air compressors, guaranteeing that the resulting products are long-lasting and well-crafted.
Molding and Pressing
Molding and pressing machines rely on air compressors to generate the force required for exact and consistent results when shaping leather into desired forms.
Spraying and Finishing
Air compressors are essential in the leather industry for painting and finishing applications. They allow for the equal distribution of colour and protective coatings, which improves the overall appearance and durability of leather items.
Maintaining Cleanliness
Air compressors are also used to keep work areas clean. The power air guns and blowers remove dust and debris, keeping the workplace clean.
Energy Efficiency in the Leather Industry
In any industry, efficiency is vital, and the leather industry is no exception. Air compressors have grown more energy-efficient, assisting leather makers in lowering their carbon footprint and operating expenses.
Variable Speed Drives (VSD)
VSD technology is commonly found in modern air compressors. This technology automatically adjusts the compressor's speed based on actual air demand, decreasing energy usage during idle periods.
Heat Recovery Systems
Heat recovery systems capture and recycle this heat for various heating processes across the facility, lowering energy consumption even further.
Conclusion
Air compressors are more than simply tools in the leather business; they are the driving force behind precision, efficiency, and quality. Air compressors improve every phase of leather manufacturing, from cutting and sewing to molding and finishing. Their adaptability, efficiency, and eco-friendly advancements make them a vital asset in the leather sector, ensuring the production of excellent leather goods that will last for generations. Air compressors are set to play an increasingly more important role in influencing the future of the leather industry as technology advances.
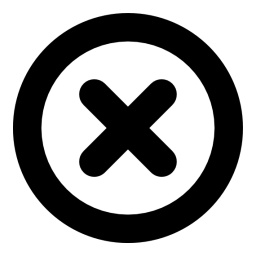
GET IN TOUCH