
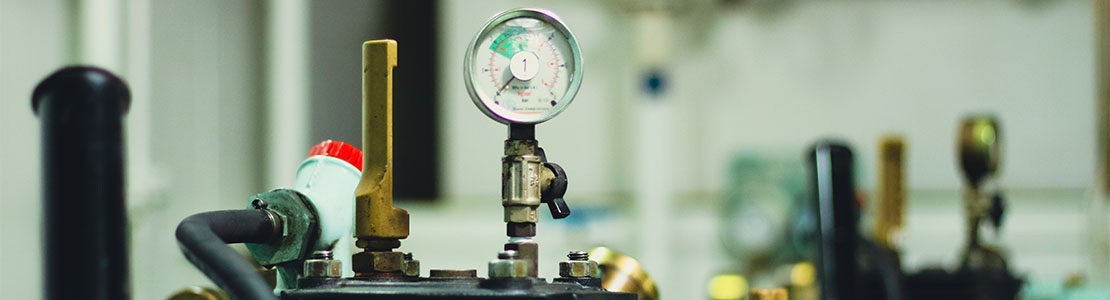
Common Problems Faced by Compressors
Many industries rely on compressors to compress air and facilitate a variety of processes. Compressors, like any mechanical equipment, can have problems. Some common issues encountered by compressors and the importance of addressing them promptly for optimal performance and longevity are discussed below:
The compressor Does Not Start / Stop or Provide Adequate Pressure
Check the power connections. Insufficient air pressure in relation to the cut-in pressure can hinder the compressor from starting. Adjusting the cut-in pressure settings may be necessary to rectify this. Lack of oil can also contribute to startup failure. Regularly monitor and maintain proper oil levels.
If a compressor does not stop operating at the cut-off point, it may be due to a faulty pressure release valve or a defective power switch. To address this, cut off the power and replace the valve.
When the compressor is running but not generating any air pressure, it is likely due to a problem with the air intake pump or a faulty gasket between the low-pressure and high-pressure compartments. Replacing these components will help restore optimal performance to your
Air Leaks
If the air compressor loses pressure after being deactivated despite having a full tank, it indicates the presence of an air leak. To locate the leak, listen for hissing sounds or feel for escaping air by running your fingers over the components. If you can't find the source, apply liquid soap to the connections and look for bubbling to pinpoint the leak. Tighten the coupler where bubbles form to seal it. Additionally, check the tank check valve as incomplete closure can cause air leaks. Clean or replace the valve as needed. Schedule a preventive maintenance program to address issues of air leaks.
Pressure Irregularities
Pressure and flow problems in air compressors can be difficult to detect since the system may seem to be functioning correctly. However, issues can arise such as excessive or insufficient air buildup, or limited pressure beyond a specific PSI. When encountering these problems, it is essential to inspect components such as the intake valve, pressure valve, gasket, piston seal, or tank check valve. If any of these components are worn out or damaged, they should be promptly replaced to restore proper functionality and performance.
Excessive Noise and Vibrations
Excessive noise from the compressor can indicate problems with the motor, worn-out bearings, loose components, or improper lubrication. Adjustments and periodic inspections can prevent worse issues.
Oil Contamination
Excessive oil in the Air Compressor's discharge is a common problem that can disrupt daily operations and harm equipment. This issue can occur due to various reasons, such as restricted intake filters, worn piston rings, overfilled oil tanks, using the wrong oil viscosity, or inverted piston rings. To resolve these problems, the intake filters should be cleaned or replaced, worn piston rings replaced, oil levels adjusted to the proper "full" mark, correct oil viscosity used, and inverted piston rings addressed with potential crankshaft replacement. By taking these corrective measures, the issue of excessive oil in the compressor's discharge can be effectively resolved, ensuring smooth and efficient operation while preventing damage to pneumatic tools and accessories.
When Trouble Shooting Does not work
If your troubleshooting efforts for your air compressor have been unsuccessful, it is advisable to seek professional assistance. Sometimes, replacing or tightening a specific part may not resolve the problem.
At MM Agencies we do Air Compressor Service as well as Air Compressor Spare Parts, our skilled technicians have the expertise to accurately diagnose and address air compressor issues. Additionally, implementing regular preventative maintenance can help identify and troubleshoot problems before they occur.Contact us today for prompt assistance.